Integration across Acuren service lines achieves cost-effective and timely asset life extension
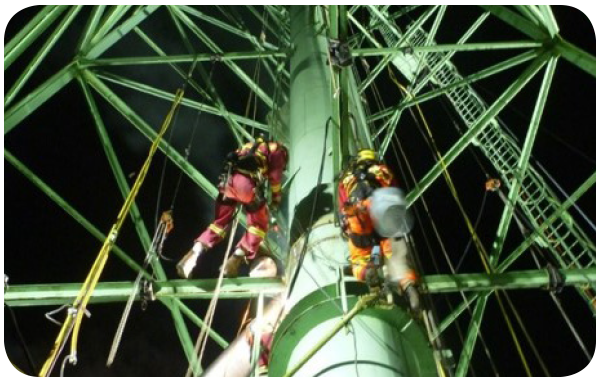
This oil and gas customer had a 60-year-old flare stack with cracking and corrosion that was approaching its end of life. Due to the cracking and corrosion thinning, there was considerable potential for failure for the flare tip and stack pipe. The cost for flare stack replacement was significant and Acuren offered a solution for life extension rather than stack replacement.
Incomplete Data Makes Planning More Challenging
This asset was part of the terminal’s legacy equipment from its original construction in 1958. Aside from some previous thickness data of the stack pipe, there was very limited history for the 250-foot tall flare stack. Acuren’s rope access technicians provided on-line inspection prior to the scheduled equipment outage to gather more information to aid in decision-making for the repair work. With this additional information, Acuren’s engineers were able to conceptualize and design a suitable repair plan.
Stack Details:
- Square tapered steel lattice support tower
- Welded construction with angle and channel sections
- Central stack pipe with corrosion thinning
- 8 horizontal clamp supports for the center flare pipe roughly every 30 feet
Various internal Acuren disciplines were required for a successful project.
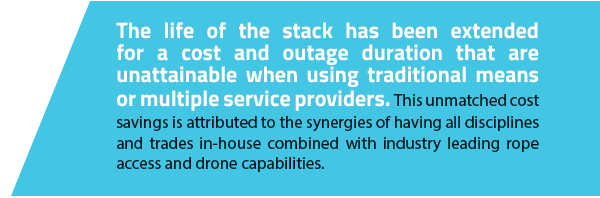
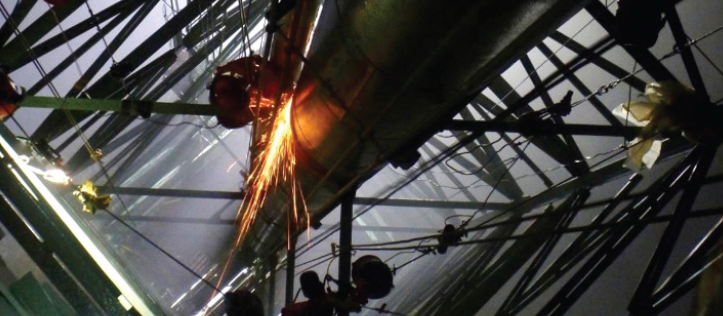
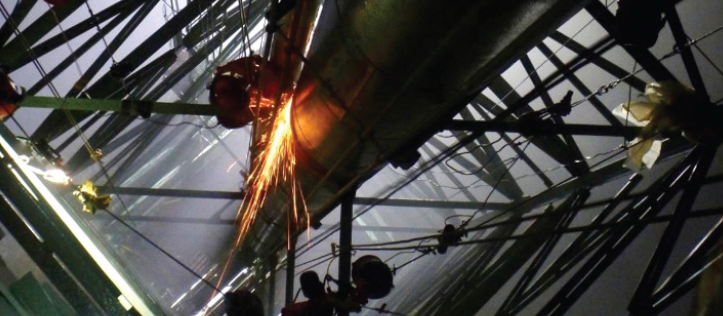
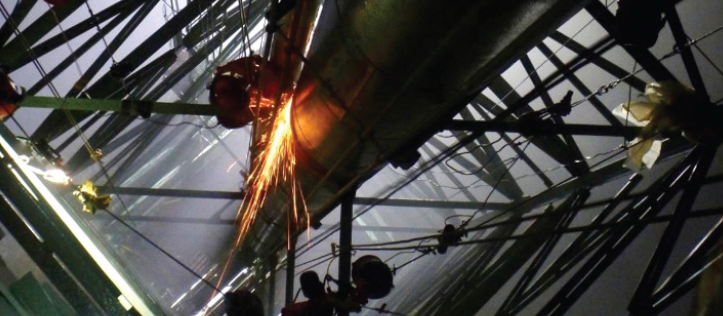
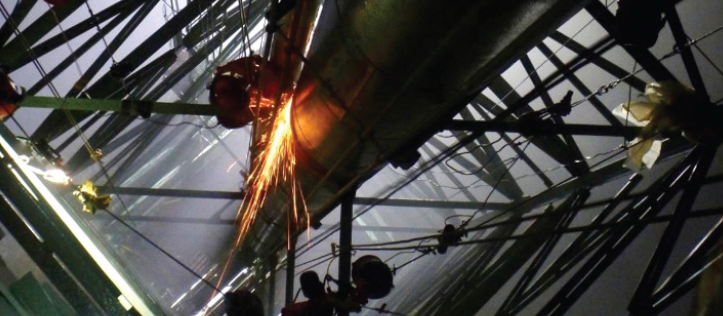
Efficiencies Gained By Use Of Drones & Rope Access
Efficiencies Gained By Use Of Drones & Rope Access
Extensive Engineering Consultation & Assessment
Acuren carried out an extensive pre-outage repair consultation/ assessment, that included creation of an outage plan, a review of the structure, the design of targeted repairs using rope access methods, material procurement, image capture and confirmation via drones, and engineering analysis to a variety of codes and methodologies while respecting site limitations and conditions:
- Review of stack based on current stack condition and applicable design codes
- Applied CSA S16 for serviceability criteria (ultimate limit states and serviceability limit states) along with other codes (ASME/API/ASCE/customer-specific)
- API 579 methodologies useful to assess limiting criteria for components and identify items for remediation
- Finite Element Analysis (FEA) modeling used
- Limit site work to 40 kph (25 mph) wind speed for safety and stack considerations
- Design/fabrication of repair components
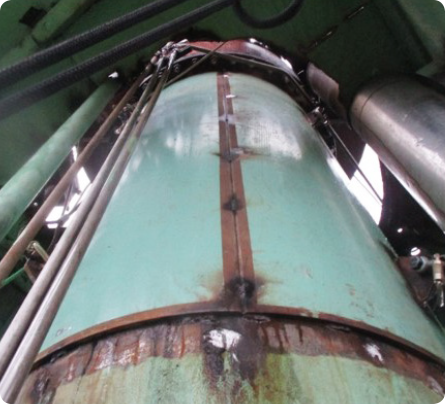
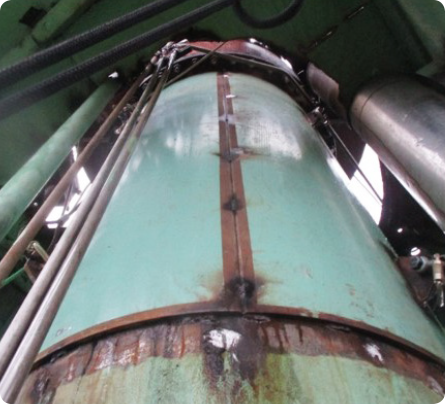
Site Inspection identified a number of concerns:
- Advanced thinning of top six (6) feet of stack pipe
- Large circumferential crack in stack pipe at flare tip flange
- Flare tip cracking
- Holes in stack pipe under clamps
- Slight progression of general thinning
- Failed ladder and piping attachments
- Cracking confirmed with internal drone
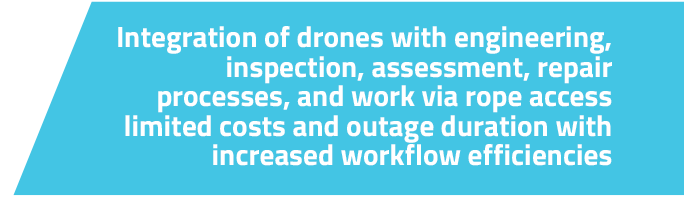
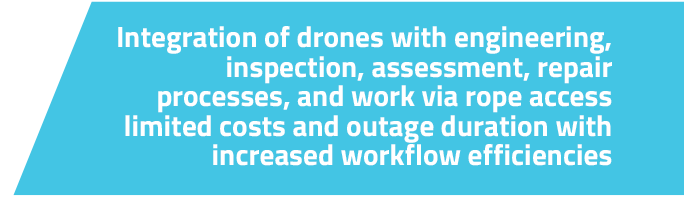
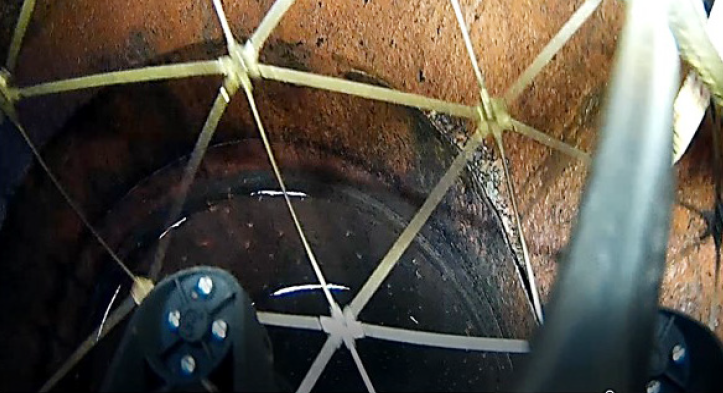
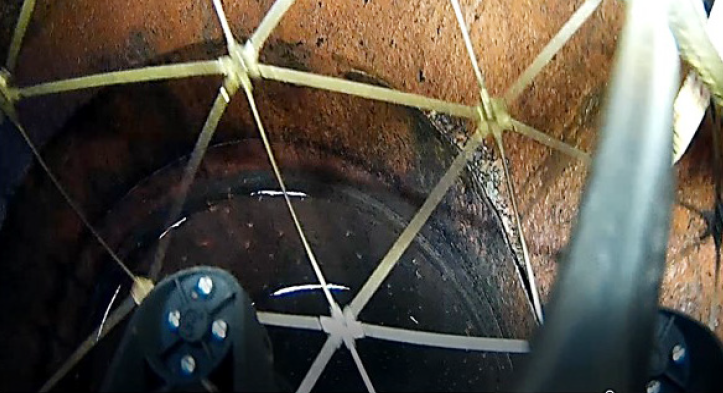
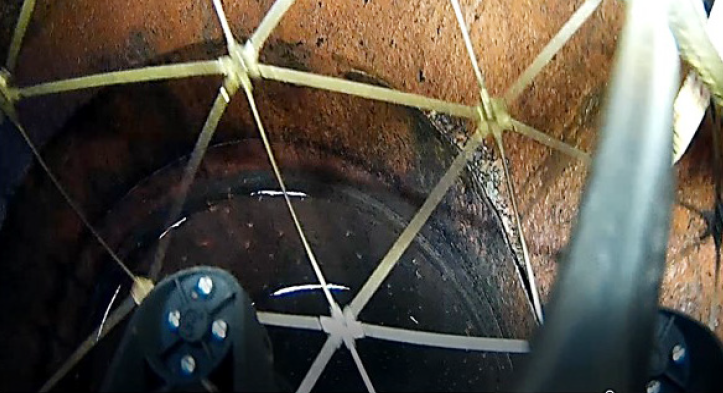
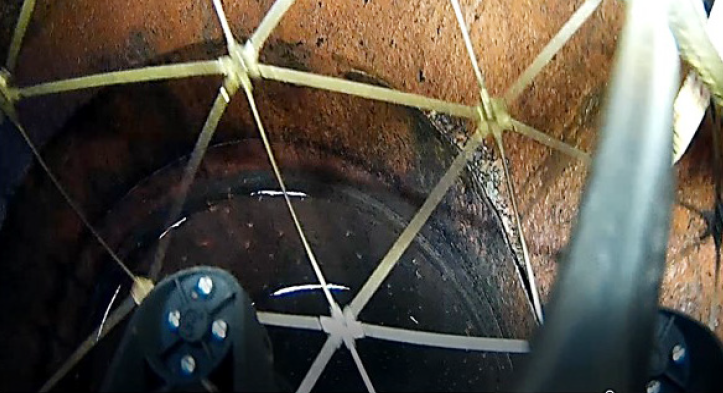
Internal view of the stack with drone
Real-Time Site Engineering Assessment & Solution Design
Real-Time Site Engineering Assessment & Solution Design
On-Site Work, Repair & Fabrication
Acuren had a 25-person crew onsite for one month which included technicians and representatives from the following integrated disciplines from across the Acuren organization:
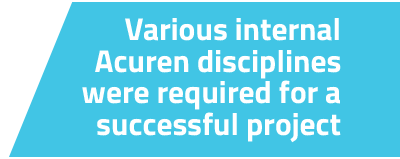
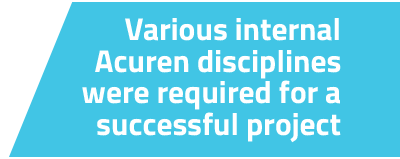
- Site engineer
- Supervisors
- Foreman
- QA/QC
- Level 3 rope technicians
- Welders
- Pipefitters
- NDT technicians
- Drone operators
- Surveyors
- Coating technicians
- Site safety
- Administrative support
- Assistants
- Helpers
This 25-person crew carried out the following work on-site:
- Welded 0.375” sleeve to address upper stack pipe thinning and flange cracking
- Welded sleeves to reinforce stack pipe at each clamp location
- New clamps installed with welding and bolted hardware per engineering design
- Repair of cracked ladder welds and attachments as well as pipe supports
- Ladder fall arrest safety system installed on all three (3) ladder sections
- Prepared installation details and drawings
- FEA conducted to verify suitability of additional found repair work
To learn more about Acuren’s personalized solutions contact us today 1-800-218-7450.