Key Takeaways
- Hydrogen looks promising, but we’re too early along the adoption curve for it to have an impact on the industry
- Feature discrimination is improving, but it’s still hard to tell the difference between problematic and non-problematic features
- Materials verification is improving rapidly, helping pipeliners ensure that what’s in the ground matches what’s described in the records
- Crack management also shows significant improvement
- COVID is still taking a bite from companies’ travel plans, with fewer operators in attendance
Industry events like the recent Pipeline Pigging and Integrity Management (PPIM) conference in Houston are great places to identify trends and understand what the industry will be focusing on in the near future, specifically in the pipeline integrity space. Acuren sent a delegation to and hosted a trade show booth at PPIM. Conversations with fellow attendees and presentations at the conference pointed to several major areas of focus. Here’s what we picked up.
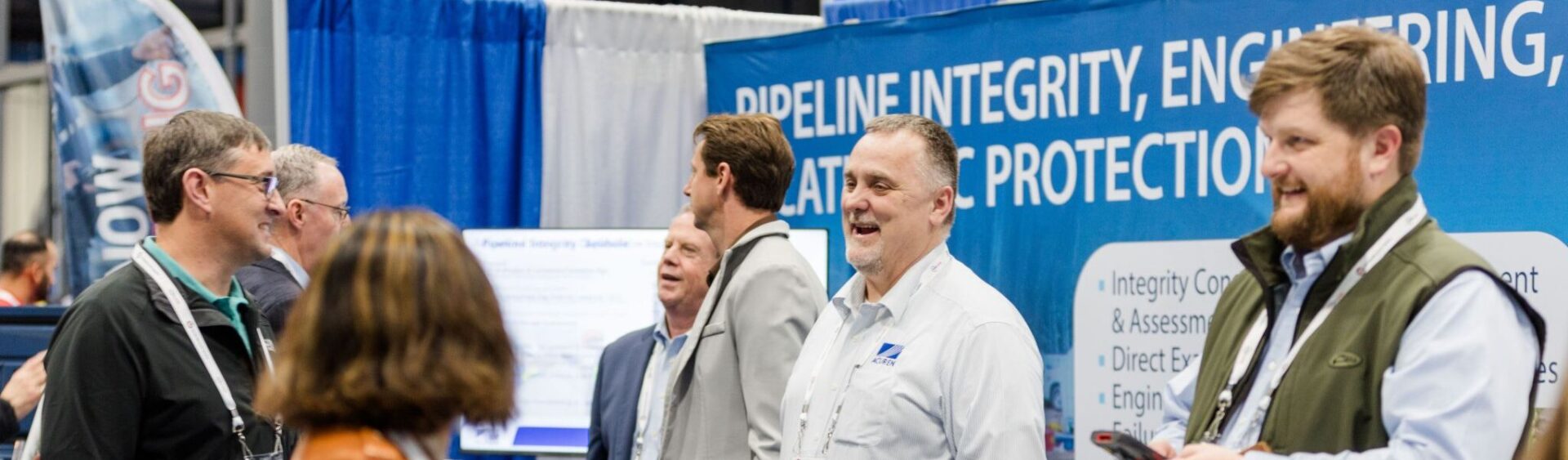
Hydrogen – fuel of the future or flash in the pan?
There’s been a lot of public discussion about the need for the world to transition away from hydrocarbons and toward other fuels such as hydrogen. This implies a need to transport that fuel from where it is generated to where it is stored or needed.
This has raised the question of whether the existing natural gas pipeline network can be repurposed for carrying hydrogen, or hydrogen blended with natural gas. There’s also been talk of how the oil and gas pipeline industry’s knowledge and experience– and possibly, rights-of-way – can support the creation of a purpose-built hydrogen network.
Our analysis from observing the industry, and from PPIM, is that we’re still very early along the hydrogen adoption curve. While it has potential for the future, there isn’t any noticeable commercial demand yet for hydrogen pipelines. One problem the industry is trying to tackle is that hydrogen causes embrittlement in carbon steel pipe, and to date there is no clear solution available for making existing pipelines H2-ready.
There’s also been talk about reducing carbon emissions by capturing carbon dioxide from industrial and other sources and transporting it to where it can be used or sequestered in deep rock formations. This is a more familiar cargo for pipelines. CO2 has long been used in industrial processes, and by the upstream sector for Enhanced Oil Recovery. CO2 pipelines are well understood, so there may be more pipeline opportunities for CO2 than for H2 in the near future.
Feature Discrimination is improving
In-line inspection tools have been in use for over 50 years, and over those decades they have grown much more capable at discovering potential problems. However, even recent generations of the technology have trouble distinguishing between problematic and non-problematic features.
Sharp-tipped cracks, which will typically grow with pressure cycles, are a serious problem but are difficult to distinguish from less problematic crack-like features. Dents that are physically coincident with pre-existing corrosion, such as where a rock has pressed against the pipe, are difficult to distinguish from dents with gouges that are likely to turn into cracks – as are often caused by a backhoe blade.
Improved technology and data analysis are now allowing better discrimination between injurious and non-injurious features, and better prioritization between injurious features. Better discrimination helps find potential problems before they become serious. But it also helps avoid over-conservativism in the form of digging features that really aren’t a problem.
We’re hopeful that the improved discrimination capabilities will increasingly allow operators to both effectively and efficiently handle threats to their pipelines’ integrity.
Materials verification is in full swing
Materials verification means making sure that what’s in the records matches the pipe in the ground, as regards characteristics like grade, strength of material, manufacturing process, diameter, and wall thickness. It’s become a growing issue in recent years, with one of the main drivers being a pipeline rupture and explosion in San Bruno, California in 2010. Inaccurate records contributed to the incident, and regulations now require pipeline operators to have adequate records to substantiate and validate the material properties of their pipelines, or to undertake verification efforts.
Sometimes the verification need arises when one company acquires another or buys some of its assets. In the past, records were often lost, or not maintained, so there’s a widespread need to determine what’s actually in the ground.
Fortunately, the technology and vendors are now available and up to the task. In-line tools can verify wall thickness. They can’t directly confirm the grade of the pipe steel, but they can detect where the grade transitions, indicating where different pipe has been used.
From that point, it’s possible to do digs and use in-the-ditch testing to directly determine other properties. This can involve using a laser to vaporize a bit of the steel to determine its chemical composition, and using a penetrometer device to measure strength. Technology for measuring toughness in the ditch is also in the works.
Another part of verification is compiling complete and accessible records. There are information technology solutions for this, but they tend to be pricey and out of practical range for small and midsize operators. And they’re not necessary for compliance – if you keep the right records and can access them when you need them, you can meet the requirements.
Crack management
As expected at PPIM, there was a lot of discussion around crack management. The first chapter of integrity management focused on detecting and dealing with corrosion and third-party damage. While those threats are still active, the technology and programs needed to manage them seem to be largely stable and mature. However, as with materials verification, the tools and methods for managing cracks (including discrimination) have come a long way in the last few years. Now we’re able to get a much better picture of the crack situation and how to deal with it.
The newest ILI tools and analysis are better able to detect and characterize crack-like features, and as mentioned in item 2, can better distinguish and prioritize between injurious and non-injurious features. For example, you now have good chance of being able to tell the difference between a problematic hook crack and a stable lack of fusion manufacturing feature.
The industry has quite a collection of models for how cracks grow with pressure cycling and fatigue; and progress seems imminent with significant scientific focus currently directed toward standardizing what the inputs to these models should be.
We’ve also noted more maturity and competition in crack repair technologies, including welded sleeves, compression sleeves, and composite wraps.
COVID continues to impact how we communicate and travel
Finally, PPIM emphasized that COVID remains a big factor in pipeline operators’ travel policies. We haven’t seen the official numbers, but there seemed to be significantly fewer operators present relative to the number of vendors.
In normal times, conferences are a great place to meet people professionally and build relationships. In this new “remote” world, it’s harder to build the trust that leads to mutually beneficial business relationships. However, as we’ve seen over the past two years, while COVID has hampered the ability to sell in traditional ways, vendors have rolled with it, trying to demonstrate technology and capabilities through video and to sell remotely.
Conclusion
Understanding these industry trends is key to maintaining pipeline integrity and staying ahead of emerging challenges. If you’re looking for expert support or have questions about our solutions, contact us today to learn how we can help.