Key Takeaways
- There is increasing pressure to reduce emissions of greenhouse gases – including fugitive emissions of natural gas and other products
- On most transmission and gathering pipelines, fittings and equipment are the most vulnerable components – valves, pig traps, sensory devices etc.
- Threaded joints are the riskiest type of connection; they tend to corrode and develop small leaks
- Flanged and bolted connections can also be vulnerable
- Generally, the most reliably gas-tight connections are welded
- Designs for new and replacement piping should minimize connections, particularly threaded and bolted joints, and use welded connections where possible
Our world is facing a growing need to reduce emissions of planet-warming greenhouse gases.
As a result, the pipeline sector is facing increasing regulatory and public pressure to reduce its impacts through unplanned or fugitive emissions. Some pipeline operators also feel regulatory pressure to manage emissions to maintain their air quality permits, which are based partly on the number and type of fittings in a facility.
At the same time, there are more tools available to track fugitive emissions, including the infrared cameras being deployed on site, in the air, and via satellite. Because detection at low concentrations is easier now, there’s a good chance that it will eventually become mandated by regulation.
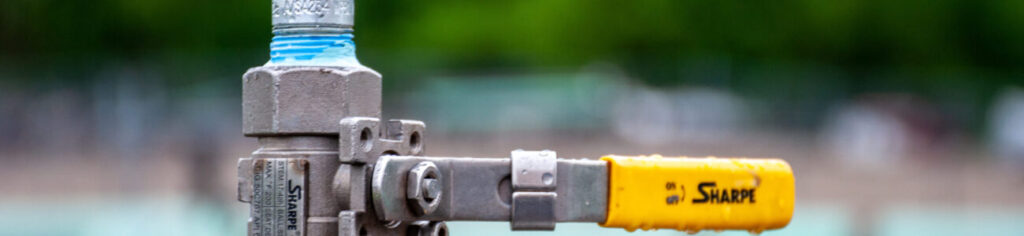
What are the weak points on your line?
While it’s possible for emissions to come from almost any part of a pipeline due to pipe or component failure, there are areas that are particularly vulnerable. Some of the most susceptible are due to attachments and fittings, such as valves and data-collection devices.
On a typical pipeline that has been in service for a while, most but not all these fittings still serve a purpose. Because of the growing importance of eliminating fugitive emissions, it’s good practice to examine your line to see if there are any fittings that were necessary at some point, but whose usefulness is now gone. See if removing unnecessary fittings is practical – particularly when the line will be shut down anyway for other work.
But often, there’s no easy way to reduce the number of fittings. This means a way must be found to minimize the leak potential for the fittings that are present.
Practical steps for reducing your risk exposure from fugitive emissions
There’s no single solution to the problem of leaks related to pipeline fixtures. It’s about design choices that minimize opportunities for leaks. Here are some principles you can follow:
Avoid placing fixtures such as valves underground
If fixtures are below grade, they can’t be easily checked for small leaks. Checking requires excavation, which takes significant time and money. It also risks damage to the fixture or the pipeline, so digging to check underground fixtures tends to be avoided and they are not done as often as those that are aboveground.
And if a fixture is out of sight, it may also tend to be out of mind. It may be quietly leaking for years, with the emissions migrating to surface and into the atmosphere, or into groundwater.
This means it’s best to not install new fixtures underground, and in the normal course of maintaining the line, relocate underground fixtures aboveground. Avoid underground flanged connections too, as these can be another source of leaks.
Minimize threaded connections
Threaded connections are convenient, quick, and don’t always have to involve a welder. But they tend to have more issues than welded connections – including corrosion and leaks around the threads. If multiple materials are involved, there can be differential expansion and contraction of different metals as the temperature changes, posing another risk of leakage.
Be careful with flanged and bolted connections
Flanged/bolted connections can also be an issue when gaskets fail, wear out, corrode, and leak. These connections may be more acceptable inside a facility or station, where it’s easier for staff to check for small-volume leaks and maybe smell fugitive emissions.
Go for welded connections when possible and practical
These connections require a welder and are harder to work with when piping needs to be modified or components need to be replaced, but the risks inherent in threaded connections can tilt the balance in favor of welded.
Design your facilities to minimize non-welded connections
This means fewer connections in general, and especially fewer threaded and flanged connections. The US-EPA counts the number of non-welded connections in calculating the risk posed by the facility for its air quality permitting. A flanged connection has a higher risk score/value, and so do threaded connections.
Design the facility so that if a welded component will need to be replaced by cutting it out and welding a new one in, there is enough space to do so without replacing other fittings or components that are still good.
In Summary
Minimize the total number of joints required; minimize underground connections, particularly fittings; and minimize the number of threaded connections as well as flanged and bolted connections. For the connections you need to keep, make as many as you can welded.
As a result, you’ll keep more product in the pipe, reduce risk to your workers from fugitive emissions, and avoid regulatory sanction. You’ll also be assured that you’re protecting our planet’s environment.
If you need help updating pipelines and facilities to be less susceptible to fugitive emissions, please reach out to us. We have decades of experience designing efficient, functional piping, and are ready to help you apply the common sense principles explained above as well as the latest technologies to your system.