Key Takeaways
- Decisions made in warm climates may not be optimal for areas with significant winters
- Design for winter can include sheltering and screening aboveground components from wind
- Learn where best to add heat-tracing cable, and about the ability to inject methanol into the gas stream, to counter the effects of low temperatures
- Consider how automation can help alert operators to problems and take action as appropriate
In the Great Texas Power Outage of February 2021, some gas facilities in that usually-warm part of the country shut down – while pipelines further north, which experienced much colder temperatures, had no trouble delivering reliable service. There are two reasons for this: Pipeline operators in northern states like Michigan have experience working in cold temperatures, and they’ve been designing pipeline systems to take those temperatures in stride.
So, as the northern climes head into winter, it’s a good time to think of how to design pipeline systems for reliable service in cold temperatures. Even if changing weather patterns send warmer temperatures our way at times, unusually cold snaps may also become part of the “new normal.”
This blog post provides six points that Acuren’s professionals have found particularly important in designing and operating pipelines to meet winter’s challenges head-on.
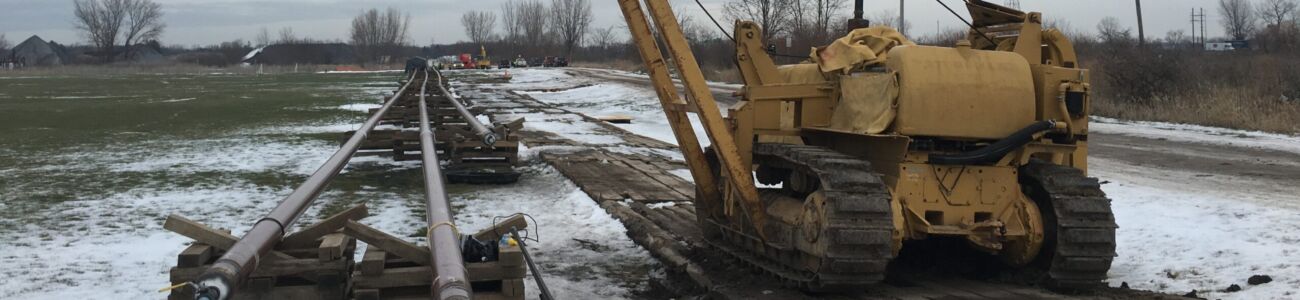
Shelter and warmth for key aboveground elements
One of the reasons that wellheads failed in Texas during the Outage was that cold winds whipped away any residual warmth in the equipment.
Much of that problem could have been avoided had the critical elements been shielded against wind-related heat loss. Even an unheated shed can provide protection against wind. A shelter also keeps snow off the piping, prevents ice buildup, and allows easier access during and after winter storms. It also protects workers against wind, rain, snow and freezing rain, which is especially helpful when performing emergency work.
Heated buildings can provide all these benefits and more – helping improve worker morale, efficiency, speed, and work quality. However, note that some buildings must be left unheated because of the need for frequent air changes for electrical safety reasons.
Design and specify for cold weather
Assumptions made while designing systems in warmer areas such as Houston or Dallas, that neglect extreme temperatures, may cause problems when cold weather hits.
Our experience has found that these problems can include inadequate expansion loops, resulting in abnormal stresses on the line as it cycles between winter and summer temperatures. Soft materials such as seals and O-rings can fall below their design temperature, shrink, and leak. Some metals become brittle with cold, and must be specified properly.
It’s important to determine which areas and equipment require heat tracing, and in what circumstances to turn it on. As we’ll see later, automation can help through sensors that can turn on the heat tracing when the temperature dips below a certain level.
In designing pipelines, it’s best to hold aboveground runs of pipe to a minimum; keep the pipe buried below the frost line as much as possible. This protects the buried pipe from temperature swings and physical damage (out of sight underground is better than out of sight, out of mind under snow).
Design gas systems to accommodate the addition of methanol to the stream to deal with water condensate – and it’s also important to deal with hydrates so they don’t obstruct flow.
Reducing gas pressure from transmission system to distribution system cools the gas, and this may condense out any water. You may need to include a way to remove water from the line and provide a heater to bring the temperature back up.
Fabricate and test for winter conditions
Pipe assemblies, valves and other components are often built and tested in the warm environment of a shop. However, materials behave differently in the cold, so it’s important to make sure that winter conditions are factored into the design and choice of components. Then, ensure that equipment is tested under winter field conditions.
Also, remember that in the warm environment of the shop, the water used to test components won’t freeze. But for field tests in sub-freezing temperatures, the test water must include glycol or another anti-freeze solution, such as salt, to prevent freezing. Even with new fabrications, this water can’t simply be dumped – it must be trucked for disposal elsewhere. This fact must be factored into your work plan and budget.
Provide access after snowfall
One aspect of design that sometimes gets missed in designing for winter is ensuring that crews can reach facilities easily and safely at all times. Aboveground facilities must be accessible, so make sure there’s room to push or dump snow removed from the roadway and parking area. Be sure that any buildings’ roofs are designed to stand up to snow – and that they don’t drop snow off a sloping roof onto personnel or equipment.
Good drainage from driving and walking surfaces will make it less likely that workers will be faced with dangerous ice during a site visit.
Design in automation where it’s useful
As we’ve discussed previously, automation – done right – can support smooth operation of the line and integrity management efforts. This might include a Supervisory Control and Data Acquisition (SCADA) system that can alert the operator to issues such as increasing pressure in part of the line, possibly indicating a frozen fixture.
Automation can be set up to respond by taking steps such as turning on heat-tracing cable or injecting methanol into the gas line. Automation can help control centers and field workers pinpoint the nature of the problem and the areas that need work. These systems can even be set to send text alerts to the mobile phones of responsible management to make sure they’re informed and can take action.
If these steps are taken to automate or remotely operate cold-weather mitigations, there may be less need for shelter to protect workers, but do consider what maintenance and servicing will still be needed, and how it will be done in winter conditions.
Get support from an experienced engineering firm
To make sure your pipelines and facilities are designed to continue operating reliably through winter weather, consider what a qualified engineering firm such as Acuren can provide:
- Design facilities that can be safely and reliably operated and maintained in harsh winter conditions
- Perform a “cold eyes review” (pun intended) to ensure that designs and specified materials are appropriate for winter
- Identify, design, and implement automated mitigations for freezing temperatures
- Analyze operational data to see if cold temperatures are a factor in issues that a line is facing
- Provide training for employees on how to deal with winter conditions
We can help provide you assurance that your lines’ throughput and integrity are all that they can be, and support safe working conditions for your field personnel.