Industrial enterprises rely on machinery to drive their operations and meet their business objectives. No matter the industry or application, the performance and reliability of this equipment directly impact the value companies derive from their assets. Maintaining optimal machine condition is crucial to sustaining profitability.
Unplanned machinery failures pose significant financial, safety, and environmental risks. Reliability engineers play a critical role in identifying, mitigating, and eliminating these failures, enhancing overall company performance. By preventing costly downtime and ensuring equipment functions at peak efficiency, reliability engineering is a key factor in maximizing asset value.
In this article, we’ll explore reliability engineering and how it can help businesses achieve operational excellence.
What Is Reliability Engineering?
Reliability engineering focuses on ensuring that machines function as intended over their life minimizing downtime and failures. The primary tasks are to analyze risks, predict potential failures, and develop strategies to mitigate the risks for the life of the asset. Ideally the assessments start during the design phase and continue throughout its life cycle.
Reliability engineers use engineering principles and data analytics to identify potential risks to machinery operation and develop maintenance strategies that mitigate the risks.
The Role of Reliability Engineering in Improving Equipment Reliability
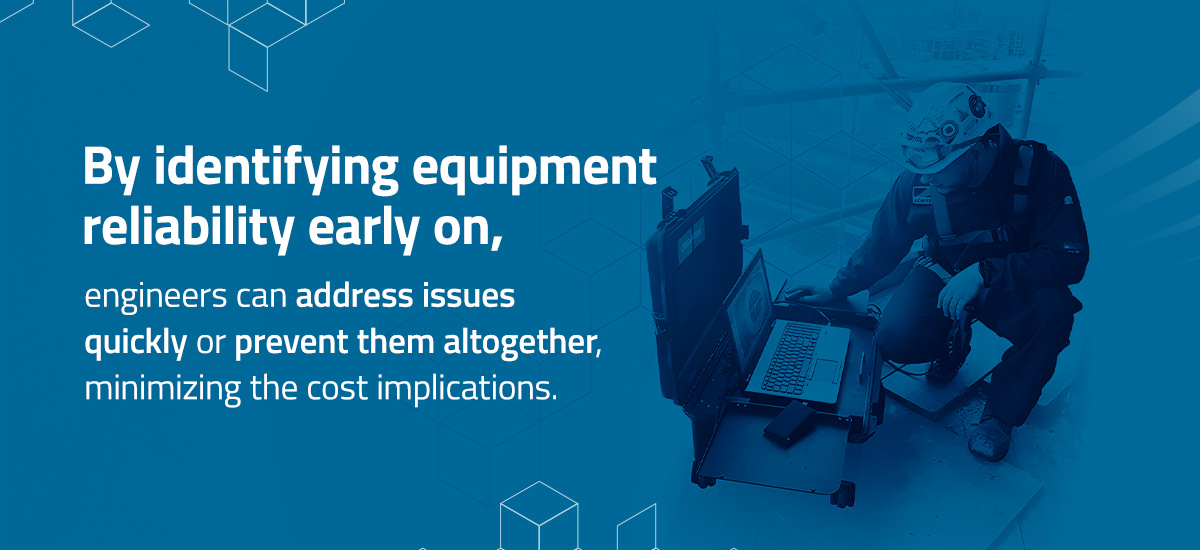
Reliability engineers are problem solvers. They interact with people, machines and systems to ensure that the optimum value is achieved from business assets. They are responsible for measuring system performance, analyzing deviations, and providing solutions to continually improve business operations.
The functions generally include involvement in all stages of the business such as strategy and planning, the assets lifecycle, risk and review, and information management.
- Strategy and Planning: Reliability engineers are often involved in creating tactical strategies that guide technical staff when making asset related decisions and plans. These can include strategies on asset risk and management, information and data systems, turnarounds and maintenance management. Reliability engineers help create the high-level programs that communicate the tactics to use when making decisions related to how assets are operated and maintained
- Front End Engineering: Reliability engineers can estimate the availability of systems and their components, provide asset maintenance strategies and estimate the cost to operate and maintain assets. For instance, by using statistical techniques to analyze equipment in similar service they can determine the system availability. Reliability Engineers also perform Reliability Centered Maintenance (RCM) assessments on new equipment that allows for upfront planning of what will be required for predictive, and preventative maintenance when the machine is operational to minimize downtime. This technique uses the FMEA technique to determine the ways in which an asset could fail, determines the probability of those failures and aligns those with the appropriate inspection technique and frequency.
- Asset Life Cycle: Proper execution of the strategies and front end engineering throughout the operation of the asset will ensure its design performance and life expectancy is achieved. The life cycle includes evaluation of acquiring the asset, operating, maintaining and disposing of the asset. Reliability engineers can add value to all aspects including calculation of costs related to each stage, using statistical techniques to analyze
- Human to Machine Interactions: Reliability engineers are often at the forefront of improvements for maintenance functions. This includes developing procedures and processes around maintenance planning and scheduling, predictive maintenance program optimization, precision maintenance, machine learning systems, and basic machine care. The interaction between machinery and the operators and maintainers is critical in the long term sustainability of equipment performance.
- Machine to Machine interactions: Reliability engineers perform diagnostics and analysis on machines and systems to ensure they are operating at peak performance. They have the ability and knowledge to step back and look at machinery issues at the system level to determine machinery interactions that may be leading to overall output.
- Root Cause Failure Analysis: Reliability engineers often steward the RCFA process and provide the final analysis report. Machinery that is performing as designed should not fail unexpectedly. When it does, the failure should be highly scrutinized to determine the underlying issues that caused the failure and drive actions to either eliminate or reduce the risk of them occurring in the future. This could be something simple that is performed as a single. The Reliability engineer is often the facilitator of this process which depending on the complexity may include operators, maintainers and other subject matter experts.
- Information Management: Reliability engineers are often part of the team to develop the systems and processes in which machinery information is stored and management. This includes computerized maintenance management systems (CMMS), asset information management, predictive maintenance databases, downtime tracking and RFCA tracking systems. Integrating these systems into cohesive machinery centric information management system is critical to providing the data needed by reliability engineers for their analysis.
Reliability Engineers in The Field
It is impossible to completely prevent failures. However, with the help of Reliability Engineers and Technicians, businesses can mitigate risks to manageable levels and prevent catastrophic losses. By identifying equipment performance issues early , maintenance can take action quickly and minimize the impact.
A specialized subset of Reliability Engineering deals specifically with rotating machinery. These highly knowledgeable engineers and technicians focus on identifying and correcting rotating machinery run-ability issues that can affect operating performance and long-term availability. Examples of when this type of work includes advanced diagnostics of rotating and static equipment issues caused by vibration excitation, in-situ balancing of all rotating components, modal analysis and designs, and advanced vibration control projects. Some of the techniques used by this team include:
- Forced response testing
- Transient data analysis
- Peak phase and amplitude
- Dynamic and static balancing
- Shaft torque measurements
- Linear displacement and strain
- Machine speed trials and baseline
- Operation deflection shape analysis
- Modal analysis
Advanced vibration control improves the operation and longevity of machinery by reducing vibrations that can cause fatigue and other failures. The team uses specialized equipment to instrument machinery, analyze the machinery’s motion, then use finite element analysis to alter the system dampening characteristics to reduce the operating vibration levels. Additionally, if resonance is an issue designs that shift the natural frequency of the structure outside the range of the forcing frequencies are also incorporated into the modifications.
Reliability Engineers are responsible for the direction and methods for rotating equipment inspection techniques because of their expertise in these technologies. Typically grouped as predictive maintenance, below are a few examples:
- Vibration analysis: By analyzing the vibration signature, engineers can identify bent shafts, mechanical looseness, defects in bearings, structural resonance, unbalance and more. This technology is also used to perform in-situ balancing of rotating machinery such as fans and rollers.
- Infrared thermography testing: This test captures infrared energy from an object’s surface and converts it into temperature. Equipment temperature typically rises before a failure occurs and IR testing is an integral part of a predictive maintenance program.
- Lubrication analysis: Lubrication analysis involves analyzing oil and grease samples to determine the condition of the lubricant and the wetted surfaces that it touches. Our team takes the results of lab testing and turns them into actionable tasks to address issues.
- Airborne Ultrasound: This technique measures the high frequency noise emitted from rotating machinery, electrical equipment or pressurized systems. This noise is interpreted as either early-stage failure, electrical discharge, or leaking/bypassing equipment depending on the application.
- Motor Testing: Testing various signatures from motors both online and offline can identify faults such as electrical unbalances, insulation condition, broken rotor bars and more.
How Reliability Engineering Improves Business Operations
Reliability engineering impact business operations throughout the strategy, planning and asset lifecycle stages. With reliability engineering, businesses can:
- Increase employee productivity: By ensuring equipment is reliable and dependable, workers can perform their tasks smoothly and efficiently with less stress. A reliable plant is also a plant that is predictable without operational chaos.
- Reduce maintenance costs: An increase in machinery reliability means a decrease in repair and maintenance costs. Emergency repairs cost significantly more in terms of the repair and the additional cost of the downtime than when predictable failures are planned during turnarounds.
- Increase safety and environmental performance: Dependable and well-maintained machines are also safe machines. Reliability engineering reduces the risk of safety and environmental incidents through ensuring equipment and people are predictable and avoiding catastrophic failures.
- Optimize asset value: The value a business realizes from its assets is directly tied to the availability of the machinery it uses, and the raw products passing through them. The impact of having support from Reliability Engineers on the availability of those machines can significantly improve the overall performance of a business.
Enhance Your Business Operations With Acuren
Reliability engineering is an essential element of asset management. It helps identify and reduce risks to equipment performance, safety and the environment for any business that owns physical assets.
Acuren offers reliability engineering services that can reduce your overall operational costs and realize maximum value from your assets. We’ll contribute to a safe work environment and provide actionable insights that optimize your resources. Contact us today to get started!