Acuren’s Ammonia System Inspection group helped a food industry giant avoid a possible shutdown. Acuren’s experts were tasked with inspecting the pipes and vessels involved in a 75,000 pound ammonia system in Arkansas.
The main concern of every ammonia system is corroded pipe that can risk the safety of employees, surroundings, and efficiency of the plant that could ultimately even cause a shutdown. Acuren’s combined testing solution helps clients avoid these risks while meeting all regulatory compliance.
Acuren used an integrated approach to support the Fortune 500 company by using a tandem of x-ray inspection methods. Digital radiography (DR) and real time radiography (RTR) was used to reveal areas of corroded pipe and areas of concern. Integrating our inspection methods can help locate corroded pipe, instead of selecting random spots to perform ultrasonic testing to check for possible corrosion, many times resulting in unnecessary testing. Additionally, a combination of x-ray inspection methods allows the client to avoid costly insulation removal to view the pipe while also avoiding damaging of the jacketing.
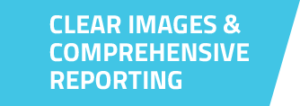
Acuren’s clear x-ray inspection images deliver precise wall thicknesses that allow the client to make an educated decision of whether to replace the pipe or not. Acuren’s reports include the client’s threshold percentages indicating compliant and non-compliant measurements for easy identification.During this project, Acuren discovered several locations of severely corroded pipe that threatened plant operations. Upon the findings, the customer followed their safety management program process that showed the percentage of wall loss exceeded the client’s set criteria. This called for immediate pipe replacement. If the location were not treated a leak could have occurred and part or all the plant would be shutdown, costing the plant downtime in production and the possibility of hurting employees and the environment.
The integrated inspection approach is part of Acuren’s 5 year NDT Mechanical Integrity Ammonia System Inspection program. Part I is Acuren’s Mechanical Integrity Visual (MI-5) followed by our NDT combined x-ray inspection methods on pipe. The MI-5 inspection is used to build and conduct the NDT services to address areas of concern.
Our integrated approach combines precise results with a planned and organized approach. Before inspections start, a carefully crafted process is followed. This starts with the naming of areas of the plant. These names are used to organize the inspection step by step. The report is prebuilt using these names and in the end the customer will choose an area name from the report to zero in on the inspection results.
To learn about Acuren’s pre-inspection report building and planning, advanced inspection methods and the training and experience of our ammonia industry technicians that has made us a leader in the Ammonia System Inspection market, visit our website or call our experts today to schedule a presentation.
Acuren’s non-invasive inspection methods provide
conclusive, visible & cost effective results
Contact us today at 1-800-218-7450 to find out more about Acuren’s integrated approach.